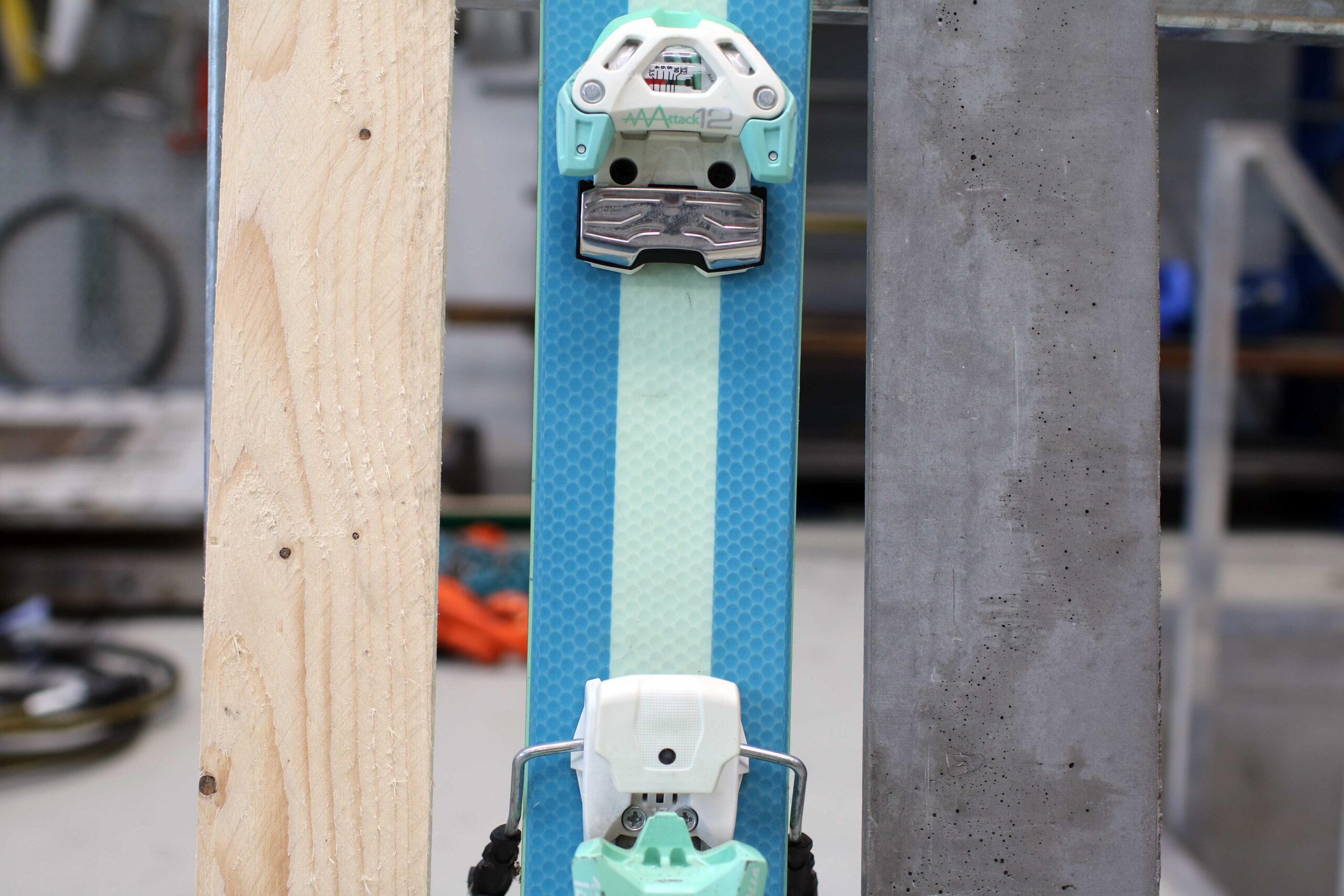
Im Labor der TU werden die Materialeigenschaften eines klassischen Skis mit Holzkern und einem Ski mit Textilbetonkern getestet © TU Wien
Textilbeton ist ein Werkstoff, der nicht nur für die Baubranche neue Perspektiven bringt. Im Labor der TU wird daran getüftelt, den typischen Holzkern im Ski mit dem neuen Material zu ersetzen. Wir verraten, welche Vorteile das bringt und wie weit die Prototypenforschung bereits ist.
Es ist schon eine lustige Vorstellung, die Piste künftig auf Beton hinunterzubrettern. Ist doch seit jeher Holz das traditionell verwendete Material für den Ski-Kern. Kein anderes Material kann dem Ski eine so gute Spannung und Elastizität verleihen, hieß es bisher. Dass es Alternativen gibt, wollen die promovierte Bauingenieurin Susanne Gmainer gemeinsam mit Philipp Preinstorfer, Forscher am Institut für Tragkonstruktionen der TU Wien, jetzt unter Beweis stellen.
Die Idee zu dieser Materialforschung kam – wie so oft in der Wissenschaft – ganz spontan. „Als ich eine Dokumentation sah, wie jemand einen Ski aus Holz selbst herstellte, dachte ich mir: Warum eigentlich Holzskier, wenn ich die guten Eigenschaften von Textilbeton nutzen kann?“ erzählt Gmainer.
Textilbeton setzt neue Maßstäbe
Ein Ski besteht generell aus rund 30 bis 50 Einzelteilen, die in bis zu 125 Arbeitsschritten einzeln bearbeitet und miteinander zu einem hochwertigen Sportgerät verbunden werden. Als klassische Bauweise, um die verschiedenen Materialien des Skis miteinander zu verbinden, gilt die „Sandwich-Bauweise. „Textilbeton kann neue Maßstäbe hinsichtlich Tragfähigkeit setzen“, ist Susanne Gmainer überzeugt. Textilien rosten nicht, lassen eine ganz dünne Betondeckung zu und sind in unterschiedlichen Rasterabständen (klein bis sehr groß) zu erhalten. Dadurch seien die Eigenschaften des Skis sehr gut beeinflussbar. Holz hingegen sei inhomogen und erlaube in der Produktion wenig Spielarten. Zudem brauche man bestimmte Sorten wie Esche oder Pappel, die mitunter schwer zu bekommen seien.
Textilbewehrte, also mit Kunst-, Glas-, Carbon- oder auch Naturfasern wie Bambus verstärkte, Betone weisen im Vergleich zu Holz bei ausreichendem Dämpfungsverhalten sehr hohe Tragfähigkeiten sowie höhere Dreh- und Biegesteifigkeiten auf. In anderen Bereichen kommt Textilbeton bereits zum Einsatz, etwa bei Fassadenplatten oder Wand- und Treppensystemen. Aber auch im Brückenbau wurden bereits neue Tragwerke aus Carbonbeton verwendet.
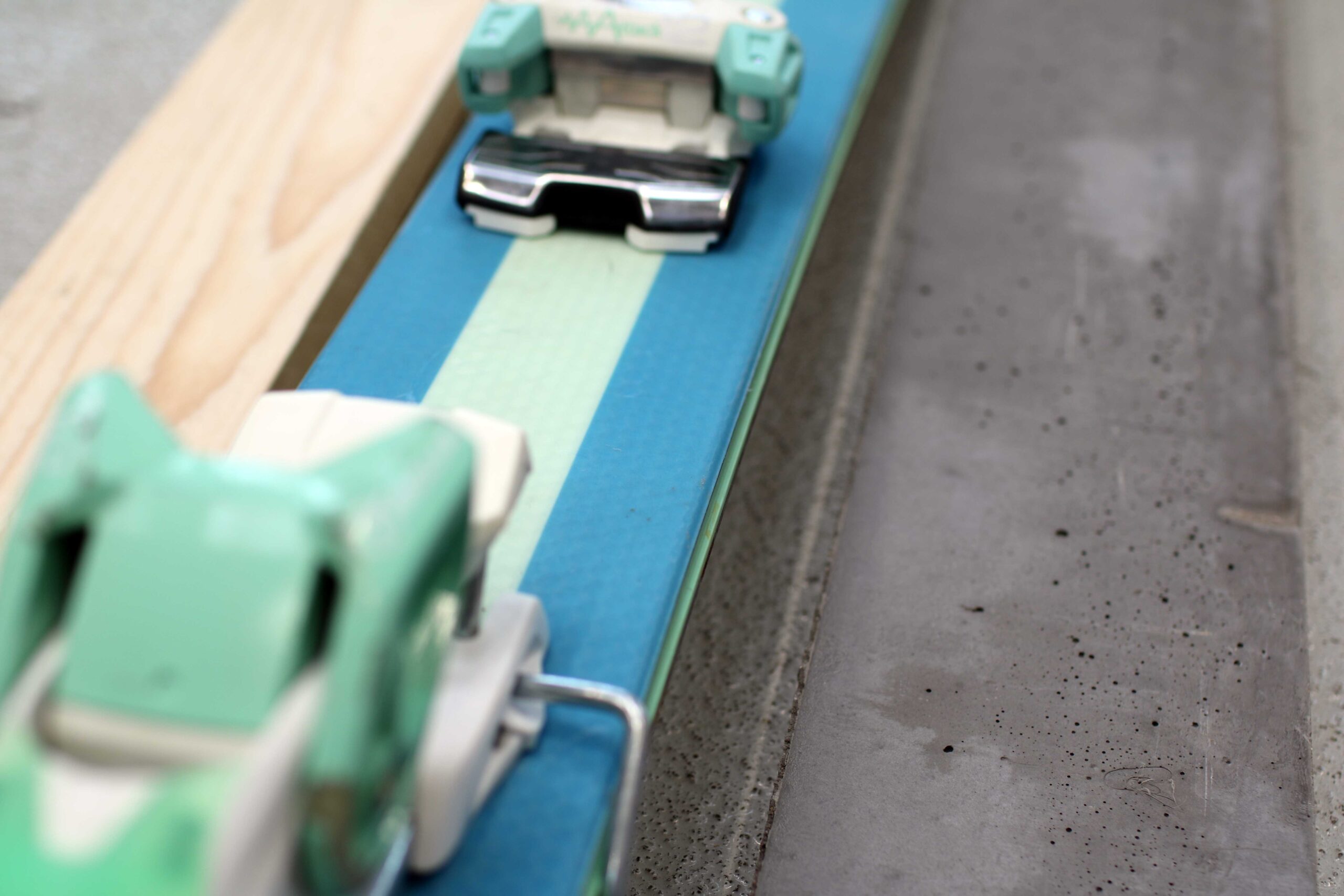
© TU Wien
Eine große Rolle spielt auch die Dauerhaftigkeit des Materials. „Beton kann mittlerweile wesentlich nachhaltiger hergestellt werden als dies vor einigen Jahren noch der Fall war. Eine Reduktion des CO2-Ausstoßes wird aufgrund der Reduktion des Klinkeranteils in der Zementherstellung bei gleichbleibender bzw. verbesserten Produkteigenschaften, sowie durch den Einsatz von Alternativbrennstoffen mit hohem Biomasseanteil erreicht“, erläutert die Forscherin. Textilbeton lasse sich zudem auch gut trennen.
Vom Prototyp bis zur Piste
Auf dem Weg vom Prototyp bis zu produktionsreifem Produkt sind schon einige Etappen geschafft. Das nationale Patent wurde im Oktober 2023 für ein „Sportgerät zum Gleiten auf Oberflächen“ erteilt. Anfang 2024 soll das letzte Arbeitspaket der Prototypenförderung des Austria Wirtschaftsservice GmbH (AWS) umgesetzt werden. Dann wird der Textilbetonskikern mit den darüber- und darunterliegenden Carbonschichten, dem Belag, den Kanten und Deckschichten zu einem fahrtauglichen Ski zusammengefügt.
Die Forschungen könnten auch für andere, ähnliche Sportgeräte wie Snowboards, Wasserski oder Wakeboards nutzbar sein. Sogar Kernelemente für Tennisschläger seien nach weiterer Entwicklungsarbeit denkbar, sagen die Forschenden. Vorerst steht aber der Ski im Mittelpunkt. Eine namhafte Skifirma hat sich bereit erklärt, den Prototypen genauer unter die Lupe nehmen.